320吨动态轨道衡计量软件的开发与实现
作者:全球MRO综合服务商 仪器仪表行业新闻来源:全球MRO仪器仪表交易网 点击数: 更新时间:2007/5/20
一、前言
我国动态轨道衡的发展已有20多年的历史,由于具有称量速度快、精度高等特点,在铁路货车计量方面得到了广泛的应用。在冶金企业中,称重对象除标准铁路四轴车外,还有各种特种类型的非标车,这些车不仅车型复杂,而且吨位较大,如各种铁水罐车,最重可达800吨以上,车辆的轴数达到八个甚至更多,给计算机模拟判车带来很多困难。
安钢2200m3高炉于2005年10月投产,为了满足生产需要,安装了一台320吨动态轨道衡用于170吨铁水罐车的计量。
二、设备硬件概况
设备硬件主要由称重台面、称重传感器、信号转换器、计算机等组成。
1、机械台面
由于计量对象是液体,采用双台面整车计量方式,消除由于铁水晃动对计量结果的影响。秤台长度的选择应考虑到动态称重时有足够的采样长度和有利于模拟判车。根据我们使用的铁水罐车的轴距尺寸,考虑到实际动态运行时的各种因素的影响,我们选择秤台长度为5300毫米,有效称量段可达1600毫米,可以确保动态计量时约有0.5秒左右的采样积分时间,根据重量信号的变化,计算机软件能比较准确识别出需秤重的信号,实现计算机模拟判车。
2、称重传感器称重传感器完成力信号到电信号的转换,根据我们的使用经验,选用PR6201/50D1型传感器,因其精度高、 长期使用稳定性好、过载能力强等优点,在动态称重上有着广泛的应用。
采用轨道衡专用称重转换器,完成对重量信号的放大和模数转换,并变成RS485信号与计算机进行数据交换。
三、系统软件的设计
1、软件平台
(1)采用Windows操作系统,具备多进程和多任务的处理能力。
(2)数据库选用MS Access和MSSQL Server2000,满足计量数据的入网要求。
(3)系统开发平台采用Delphi语言。Delphi具有强大的数据库支持功能,程序结构严谨,代码执行效率高,很适合开发Windows应用程序。
2、应用程序的分析开发动态轨道衡计量系统软件是整个轨道衡的核心和关键。系统在基本硬件的支持下,利用计算机实现对重量信号的分析与处理,获得秤量结果。
(1)重量信号的采集通过计算机的RS232接口实现和称重转换器的数据交换,读取传感器输出的重量信号。
(2)数据库设计本地数据库使用Access2000关系型数据库,并设计三个表BaseData Table、 Operate Table、 LogRecord Table,分别存放基础数据、SQI操作语句、日志。为了满足计量数据的入网要求,我们同时安装了MS SQL Server2000,创建和Access相同的数据库结构,通过存储过程将数据保存到集群服务器。
(3)模拟判车的实现
判车程序是整个计量软件的核心,一般有两种方式:①全模拟逻辑判车,即根据重量信号的变化来识别哪一段数据是我们所需要的重量信号,过滤掉不需要的车头、轴重等信号。对于铁路标准四轴货车,现在普遍采用这种判车方式。②轮开关判车方式,在称重台面的钢轨上加装接近开关,通过计算轴数确定有效称量段,其缺点是需安装轮开关,并且开关的故障率相对较高。对特种类型的轨道衡由于重量信号波型复杂,模拟判车难度较大,一般采用开关判车。
我们根据320吨轨道衡的数据特点,自主开发了轨道衡动态计量程序,实现了计算机软件全模拟逻辑判车,并根据实际生产要求,逐步解决了170吨八轴罐车和原来的四轴罐车混编使用时的车型、重量自动识别等难题。
动态计量程序的工作原理是:程序运行后,首先进行初始化操作,启动数据采集程序,每10ms对秤台的重量信号采集一次,并根据重量信号的变化,自动识别需称重的前后转向架信号,经数字滤波、非线性误差修正等一系列数据处理后,计算出每一节车的重量。
车头识别:我公司采用的机车为GK型四轴车,同时有两根轴上秤台,机车重量小于100吨,可以根据机车的轴数和重量在程序中自动滤除。
八轴罐车识别:八轴车的每根轴上下秤台产生的信号波形特征明显,只需找出前后转向架分别同时在秤台的数据段,进行积分,求出整车重量。
四轴罐车的识别:四轴罐车的轴距为1350毫米,内轴距2700毫米,从波形中可以看出,重量信号中分别会出现两根轴(1 2)和三根轴(1 2 3、2 3 4)的重量,第三个轴下和第四根轴上之间约有100毫米的长度,波形当中会出现一个下跳尖峰,根据此特征可以判断是否是四轴罐车。我们取1 2 3轴和2 3 4轴的重量信号为有效秤量段,由于其重量信号为六根轴的重量和,需转换为四根轴的重量才是整车重量。
特种轨道衡车辆的识别与标准四轴货车差别很大,因为标准车的重量波形中两个转向架之间会有信号回零时间,根据此特征就很容易得到一节车的前架和后架重量,而非标车轴数较多,转向架与转向架(或车与车之间)没有回零时间,因此模拟判车难度较大。
轴上下秤台的识别:一般直接采用重量信号变化比例或取两段数据的平均值的变化比例来判断。这种方法适用于振动幅度较小的情况下。小于100吨的轨道衡其重量信号中由于振动引起的交流成分幅度较小,一般小于10%。对于大于100吨的轨道衡,有时受重量、速度、车辆状况等方面的影响,动态计量时振动幅度很大。特别是液态计量时振动幅度最大能达到50%以上。采用常规的对动态曲线的上升沿和下降沿进行识别就会出现错误。我公司的钢锭库200吨轨道衡虽然计量对象为钢坯、钢锭等固体物资,但由于受动态计量时多种因素的影响,仍然多次出现过振动很大的波形,造成计量数据失准或丢车。其原因就是振动幅度过大造成判车错误。有时把轴重量当成转向架重量,计量结果为实际重量的1/2或3/4。在近几年轨道衡的软件开发过程中,我们逐步采用了取动态曲线的极值点(最大值或最小值)的方法很好地解决了这一难题。在判车过程中,查找每一个极值点,根据极值点(或极值点之间数据平均)的值进行曲线的上下沿识别。
数字滤波:动态计量时,重量信号中由于震动和铁水的晃动引起的交流成分很大,如不进行数字滤波,将引进很大误差,一般采用取极值区间的方法进行数字滤波,在极值区间内取积分平均。
(4)多线程应用
计算机多线程技术通常应用于几个操作必须同时进行不能等待的情况,或者在进行一些费时的操作时,用另一个线程来处理,以免用户等待。使用多线程的目的就在于:使自己的程序可以同时处理很多任务而只消耗很少的时间。轨道衡动态计量过程中要求在对重量信号采集的同时,进行模拟数据判车、数字滤波、计算重量、速度、显示计量结果、绘制动态曲线等,双台面或多台面轨道衡要同时处理几个秤台的数据。采用多线程技术,可以将这些任务交给不同的线程去处理,并分配不同优先级别,如数据处理和逻辑判车线程享有较高的级别,显示曲线线程具有较低的优先级别。
四、存在的问题及解决办法
通过近几个月的使用,我们发现存在以下几个方面的问题,容易造成计量误差。
1、称重转换器或驱动程序存在的问题
我们现在使用的称重转换器采用RS485接口和计算机进行通讯,其主要问题是计量过程中采集数据丢失造成实时数据不完整、定时不准、数据不同步等,造成程序无法正确识别。这些问题主要是转换器本身或驱动程序引起,在使用这种转换器的其他轨道衡上也发现过类似问题。开发这种类型转换器的目的是为了解决Windows多任务操作系统下数据的输人输出和实时数据采集等问题,但根据近几年我们的使用效果看并不是十分理想。
在DOS操作系统下使用直接进行I/O输入输出的称重转换器极少会发生数据丢失和不同步现象。在Windows操作系统下,使用并行输入输出的称重转换器,通过计算机软件直接读取I/O数据,同样能达到很高的采样精度,满足轨道衡毫秒级实时数据采集的要求,但需要解决以下两个方面的问题:
(1)实时数据采集
根据动态称重计量的需求,应达到毫秒级的采样精度,Windows系统不是实时操作系统,虽然提供了定时器事件,但时间间隔小于55ms时精度很低,要达到10ms以上的采样精度很不可靠。Windows系统为用户提供了具有较高精度的多媒体定时器函数可以得到精确记时,完全能够满足要求。
(2)计算机并行数据的输入输出
通过对计算机I/O端口的读写,实现对转换器数据的读取。在Windows2000/NT系统下为保证系统的安全,不允许用户直接进行I/O操作,因此必须编写设备驱动程序,一般有两种办法,一是自己编写设备驱动程序,或者使用可以直接进行I/0操作的软件。
2、动态计量过程中曲线不规则是造成丢车的另一原因八轴罐车计量时,每根轴上下秤台时的重量变化只有整车重量的l/8, 如果速度比较恒定、车辆振动小波形规则,模拟判车应该准确。计量过程中如果出现变速加上振动幅度过大,振动频率很低,有时就会出现不规则的畸变波形,程序无法正确识别。
解决办法:增加轮开关,利用开关判车。对于八轴车容易实现,当八轴罐车和四轴罐车混编使用时,完全由开关判车比较困难,可以考虑采用模拟加开关的方法。
五、结束语
动态轨道衡的逻辑模拟判车是动态轨道衡软件设计的难点和重点,各轨道衡生产厂家在这方面的技术保密。在Windows操作系统下,要编写出优秀的计量程序需要掌握实时数据采集、数据输入输出、数据库、多线程应用等Windows编程技术。我们通过我公司单台面、双台面标准和非标准动态轨道衡逻辑模拟判车技术的研究探索,形成了具有自身特点的判车技术,较好地解决了目前工厂用动态轨道衡数据采集处理中的技术问题,满足了计量需求。
我国动态轨道衡的发展已有20多年的历史,由于具有称量速度快、精度高等特点,在铁路货车计量方面得到了广泛的应用。在冶金企业中,称重对象除标准铁路四轴车外,还有各种特种类型的非标车,这些车不仅车型复杂,而且吨位较大,如各种铁水罐车,最重可达800吨以上,车辆的轴数达到八个甚至更多,给计算机模拟判车带来很多困难。
安钢2200m3高炉于2005年10月投产,为了满足生产需要,安装了一台320吨动态轨道衡用于170吨铁水罐车的计量。
二、设备硬件概况
设备硬件主要由称重台面、称重传感器、信号转换器、计算机等组成。
1、机械台面
由于计量对象是液体,采用双台面整车计量方式,消除由于铁水晃动对计量结果的影响。秤台长度的选择应考虑到动态称重时有足够的采样长度和有利于模拟判车。根据我们使用的铁水罐车的轴距尺寸,考虑到实际动态运行时的各种因素的影响,我们选择秤台长度为5300毫米,有效称量段可达1600毫米,可以确保动态计量时约有0.5秒左右的采样积分时间,根据重量信号的变化,计算机软件能比较准确识别出需秤重的信号,实现计算机模拟判车。
2、称重传感器称重传感器完成力信号到电信号的转换,根据我们的使用经验,选用PR6201/50D1型传感器,因其精度高、 长期使用稳定性好、过载能力强等优点,在动态称重上有着广泛的应用。
采用轨道衡专用称重转换器,完成对重量信号的放大和模数转换,并变成RS485信号与计算机进行数据交换。
三、系统软件的设计
1、软件平台
(1)采用Windows操作系统,具备多进程和多任务的处理能力。
(2)数据库选用MS Access和MSSQL Server2000,满足计量数据的入网要求。
(3)系统开发平台采用Delphi语言。Delphi具有强大的数据库支持功能,程序结构严谨,代码执行效率高,很适合开发Windows应用程序。
2、应用程序的分析开发动态轨道衡计量系统软件是整个轨道衡的核心和关键。系统在基本硬件的支持下,利用计算机实现对重量信号的分析与处理,获得秤量结果。
(1)重量信号的采集通过计算机的RS232接口实现和称重转换器的数据交换,读取传感器输出的重量信号。
(2)数据库设计本地数据库使用Access2000关系型数据库,并设计三个表BaseData Table、 Operate Table、 LogRecord Table,分别存放基础数据、SQI操作语句、日志。为了满足计量数据的入网要求,我们同时安装了MS SQL Server2000,创建和Access相同的数据库结构,通过存储过程将数据保存到集群服务器。
(3)模拟判车的实现
判车程序是整个计量软件的核心,一般有两种方式:①全模拟逻辑判车,即根据重量信号的变化来识别哪一段数据是我们所需要的重量信号,过滤掉不需要的车头、轴重等信号。对于铁路标准四轴货车,现在普遍采用这种判车方式。②轮开关判车方式,在称重台面的钢轨上加装接近开关,通过计算轴数确定有效称量段,其缺点是需安装轮开关,并且开关的故障率相对较高。对特种类型的轨道衡由于重量信号波型复杂,模拟判车难度较大,一般采用开关判车。
我们根据320吨轨道衡的数据特点,自主开发了轨道衡动态计量程序,实现了计算机软件全模拟逻辑判车,并根据实际生产要求,逐步解决了170吨八轴罐车和原来的四轴罐车混编使用时的车型、重量自动识别等难题。
动态计量程序的工作原理是:程序运行后,首先进行初始化操作,启动数据采集程序,每10ms对秤台的重量信号采集一次,并根据重量信号的变化,自动识别需称重的前后转向架信号,经数字滤波、非线性误差修正等一系列数据处理后,计算出每一节车的重量。
车头识别:我公司采用的机车为GK型四轴车,同时有两根轴上秤台,机车重量小于100吨,可以根据机车的轴数和重量在程序中自动滤除。
八轴罐车识别:八轴车的每根轴上下秤台产生的信号波形特征明显,只需找出前后转向架分别同时在秤台的数据段,进行积分,求出整车重量。
四轴罐车的识别:四轴罐车的轴距为1350毫米,内轴距2700毫米,从波形中可以看出,重量信号中分别会出现两根轴(1 2)和三根轴(1 2 3、2 3 4)的重量,第三个轴下和第四根轴上之间约有100毫米的长度,波形当中会出现一个下跳尖峰,根据此特征可以判断是否是四轴罐车。我们取1 2 3轴和2 3 4轴的重量信号为有效秤量段,由于其重量信号为六根轴的重量和,需转换为四根轴的重量才是整车重量。
特种轨道衡车辆的识别与标准四轴货车差别很大,因为标准车的重量波形中两个转向架之间会有信号回零时间,根据此特征就很容易得到一节车的前架和后架重量,而非标车轴数较多,转向架与转向架(或车与车之间)没有回零时间,因此模拟判车难度较大。
轴上下秤台的识别:一般直接采用重量信号变化比例或取两段数据的平均值的变化比例来判断。这种方法适用于振动幅度较小的情况下。小于100吨的轨道衡其重量信号中由于振动引起的交流成分幅度较小,一般小于10%。对于大于100吨的轨道衡,有时受重量、速度、车辆状况等方面的影响,动态计量时振动幅度很大。特别是液态计量时振动幅度最大能达到50%以上。采用常规的对动态曲线的上升沿和下降沿进行识别就会出现错误。我公司的钢锭库200吨轨道衡虽然计量对象为钢坯、钢锭等固体物资,但由于受动态计量时多种因素的影响,仍然多次出现过振动很大的波形,造成计量数据失准或丢车。其原因就是振动幅度过大造成判车错误。有时把轴重量当成转向架重量,计量结果为实际重量的1/2或3/4。在近几年轨道衡的软件开发过程中,我们逐步采用了取动态曲线的极值点(最大值或最小值)的方法很好地解决了这一难题。在判车过程中,查找每一个极值点,根据极值点(或极值点之间数据平均)的值进行曲线的上下沿识别。
数字滤波:动态计量时,重量信号中由于震动和铁水的晃动引起的交流成分很大,如不进行数字滤波,将引进很大误差,一般采用取极值区间的方法进行数字滤波,在极值区间内取积分平均。
(4)多线程应用
计算机多线程技术通常应用于几个操作必须同时进行不能等待的情况,或者在进行一些费时的操作时,用另一个线程来处理,以免用户等待。使用多线程的目的就在于:使自己的程序可以同时处理很多任务而只消耗很少的时间。轨道衡动态计量过程中要求在对重量信号采集的同时,进行模拟数据判车、数字滤波、计算重量、速度、显示计量结果、绘制动态曲线等,双台面或多台面轨道衡要同时处理几个秤台的数据。采用多线程技术,可以将这些任务交给不同的线程去处理,并分配不同优先级别,如数据处理和逻辑判车线程享有较高的级别,显示曲线线程具有较低的优先级别。
四、存在的问题及解决办法
通过近几个月的使用,我们发现存在以下几个方面的问题,容易造成计量误差。
1、称重转换器或驱动程序存在的问题
我们现在使用的称重转换器采用RS485接口和计算机进行通讯,其主要问题是计量过程中采集数据丢失造成实时数据不完整、定时不准、数据不同步等,造成程序无法正确识别。这些问题主要是转换器本身或驱动程序引起,在使用这种转换器的其他轨道衡上也发现过类似问题。开发这种类型转换器的目的是为了解决Windows多任务操作系统下数据的输人输出和实时数据采集等问题,但根据近几年我们的使用效果看并不是十分理想。
在DOS操作系统下使用直接进行I/O输入输出的称重转换器极少会发生数据丢失和不同步现象。在Windows操作系统下,使用并行输入输出的称重转换器,通过计算机软件直接读取I/O数据,同样能达到很高的采样精度,满足轨道衡毫秒级实时数据采集的要求,但需要解决以下两个方面的问题:
(1)实时数据采集
根据动态称重计量的需求,应达到毫秒级的采样精度,Windows系统不是实时操作系统,虽然提供了定时器事件,但时间间隔小于55ms时精度很低,要达到10ms以上的采样精度很不可靠。Windows系统为用户提供了具有较高精度的多媒体定时器函数可以得到精确记时,完全能够满足要求。
(2)计算机并行数据的输入输出
通过对计算机I/O端口的读写,实现对转换器数据的读取。在Windows2000/NT系统下为保证系统的安全,不允许用户直接进行I/O操作,因此必须编写设备驱动程序,一般有两种办法,一是自己编写设备驱动程序,或者使用可以直接进行I/0操作的软件。
2、动态计量过程中曲线不规则是造成丢车的另一原因八轴罐车计量时,每根轴上下秤台时的重量变化只有整车重量的l/8, 如果速度比较恒定、车辆振动小波形规则,模拟判车应该准确。计量过程中如果出现变速加上振动幅度过大,振动频率很低,有时就会出现不规则的畸变波形,程序无法正确识别。
解决办法:增加轮开关,利用开关判车。对于八轴车容易实现,当八轴罐车和四轴罐车混编使用时,完全由开关判车比较困难,可以考虑采用模拟加开关的方法。
五、结束语
动态轨道衡的逻辑模拟判车是动态轨道衡软件设计的难点和重点,各轨道衡生产厂家在这方面的技术保密。在Windows操作系统下,要编写出优秀的计量程序需要掌握实时数据采集、数据输入输出、数据库、多线程应用等Windows编程技术。我们通过我公司单台面、双台面标准和非标准动态轨道衡逻辑模拟判车技术的研究探索,形成了具有自身特点的判车技术,较好地解决了目前工厂用动态轨道衡数据采集处理中的技术问题,满足了计量需求。
(本文来源:全球仪器仪表MRO网)
- 上一篇仪器仪表行业新闻: 我国每年需要6000万台仪器仪表
- 下一篇仪器仪表行业新闻: 美国发明:音频仪器能“听”出皮肤癌细胞
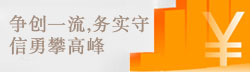